Comprehending the Key Components and Repair Approaches for Product Packaging Equipment Upkeep
Efficient upkeep of packaging devices pivots on an extensive understanding of their vital components, including the framework, drive system, and securing mechanisms. Recognizing typical upkeep concerns, coupled with the implementation of preventative methods and repairing strategies, can considerably improve maker integrity.
Key Components of Packaging Devices
Product packaging equipments include several essential elements that interact to ensure efficient and reliable product packaging procedures. At the core of these devices is the structure, which offers architectural integrity and houses the different operating components. The drive system, frequently a combination of motors and gears, assists in the movement of parts, enabling specific procedure throughout the product packaging cycle.
An additional important part is the conveyor system, which transports products through various stages of the packaging process. This is often enhanced by sensing units and controls that keep an eye on the setting and speed of things, making certain synchronization and decreasing mistakes. The filling system is crucial for properly giving the best quantity of product right into plans, whether in liquid, powder, or solid form.
Securing devices, including warm sealants or sticky applicators, play an important function in securing bundles, protecting against contamination and expanding rack life. Furthermore, classifying systems are indispensable for supplying required item info, making sure compliance with guidelines. Finally, the control board, outfitted with user-friendly user interfaces, enables drivers to handle machine functions, display performance, and make modifications as required, guaranteeing ideal productivity and effectiveness in packaging procedures.
Usual Maintenance Problems
Effective procedure of product packaging makers counts greatly on routine maintenance to protect against usual issues that can disrupt production. Amongst these problems, mechanical deterioration is widespread, particularly in elements like seals, motors, and conveyors, which can lead to unexpected downtimes. Furthermore, misalignment of parts can lead to inefficient operation, causing products to be inaccurately packaged or damaged during the process.
An additional usual upkeep problem involves the buildup of dirt and debris, which can disrupt the device's sensing units and moving components. packaging machine repair service. This not only impacts performance however can additionally position safety risks. Lubrication failings can lead to raised rubbing, resulting in overheating and eventual element failing.
Electrical troubles, commonly stemming from loose connections or damaged circuitry, can interrupt machinery features, bring about substantial production delays. Lastly, software program problems due to outdated programs or inappropriate setups can hinder the maker's operation, necessitating prompt intervention. Attending to these common upkeep issues proactively is important for guaranteeing ideal efficiency and longevity of packaging machinery.
Preventative Maintenance Techniques
Applying preventative upkeep approaches is crucial for maintaining the effectiveness and reliability of product packaging makers. These approaches incorporate a methodical strategy to maintenance, concentrating on the normal evaluation and maintenance of equipment to preempt potential failures. By sticking to an arranged upkeep program, operators can determine wear important site and tear on parts before they cause substantial break downs.
Crucial element of a preventative maintenance strategy consist of routine inspections, part, lubrication, and cleansing replacements based upon manufacturer recommendations. Making use of checklists can simplify this procedure, making certain that no vital tasks are forgotten. Furthermore, preserving precise records of upkeep activities help in tracking the device's performance gradually, assisting in educated decision-making concerning future upkeep requirements.
Educating team on the value of preventative maintenance enhances compliance and fosters a culture of proactive care. Implementing a predictive maintenance component, making use of information analytics and sensing unit innovation, can even more maximize machinery performance by forecasting failings before they occur.
Fixing Techniques
When confronted with breakdowns or ineffectiveness in packaging makers, employing organized troubleshooting strategies is important for recognizing and settling problems promptly. The primary step in efficient troubleshooting is to establish a clear understanding of the machine's functional parameters and efficiency metrics. This entails examining the maker's requirements, in addition to any error codes or alerts shown.
Following, drivers need to carry out an aesthetic evaluation, looking for noticeable signs of damages, wear, or imbalance. This usually consists of examining sensing units, belts, and gears to pinpoint prospective reasons for malfunction. Collecting functional data, such as production rates and downtime logs, can likewise offer understandings into repeating issues.
Once prospective troubles are identified, utilizing a logical strategy to separate the origin is vital. This may require screening specific parts or systems in a regulated fashion. Participating in conversations with operators who interact with the equipment regularly can yield useful responses about uncommon habits or patterns.

Repair Service and Substitute Finest Practices
A thorough understanding of fixing and substitute best her response techniques is essential for maintaining the durability and efficiency of packaging equipments. On a regular basis evaluating the condition of device parts permits timely treatment, stopping more substantial problems that can lead to expensive downtimes.
When repairs are required, it is necessary to use OEM (Original Equipment Manufacturer) parts to make certain compatibility and efficiency. This not just protects the integrity of the device but additionally upholds service warranty arrangements. Furthermore, it is recommended to maintain a stock of critical extra parts to facilitate quick replacements and decrease functional disruptions.
For complex repairs, engaging certified specialists with specialized training in packaging machinery is suggested. They possess the expertise to detect problems accurately and carry out fixings efficiently. Additionally, recording all repair service activities and parts replacements is vital for keeping an extensive maintenance history, which can assist in future troubleshooting.
Lastly, informative post applying a proactive technique, consisting of normal assessments and predictive maintenance methods, enhances the reliability of product packaging equipments. By adhering to these best practices, services can guarantee ideal equipment performance, reduce functional threats, and extend devices life-span.

Conclusion
In verdict, a complete understanding of product packaging machine parts and effective upkeep strategies is essential for optimal efficiency. By applying these methods, organizations can make certain the long life and effectiveness of packaging makers, inevitably adding to boosted operational performance and reduced expenses (packaging machine repair service).
Reliable maintenance of packaging makers pivots on a detailed understanding of their vital components, consisting of the framework, drive system, and securing systems.Reliable procedure of packaging machines depends greatly on routine maintenance to avoid usual problems that can disrupt manufacturing.Carrying out preventative upkeep techniques is critical for maintaining the effectiveness and reliability of product packaging makers. Furthermore, maintaining exact records of upkeep tasks aids in tracking the equipment's efficiency over time, assisting in notified decision-making relating to future maintenance requirements.
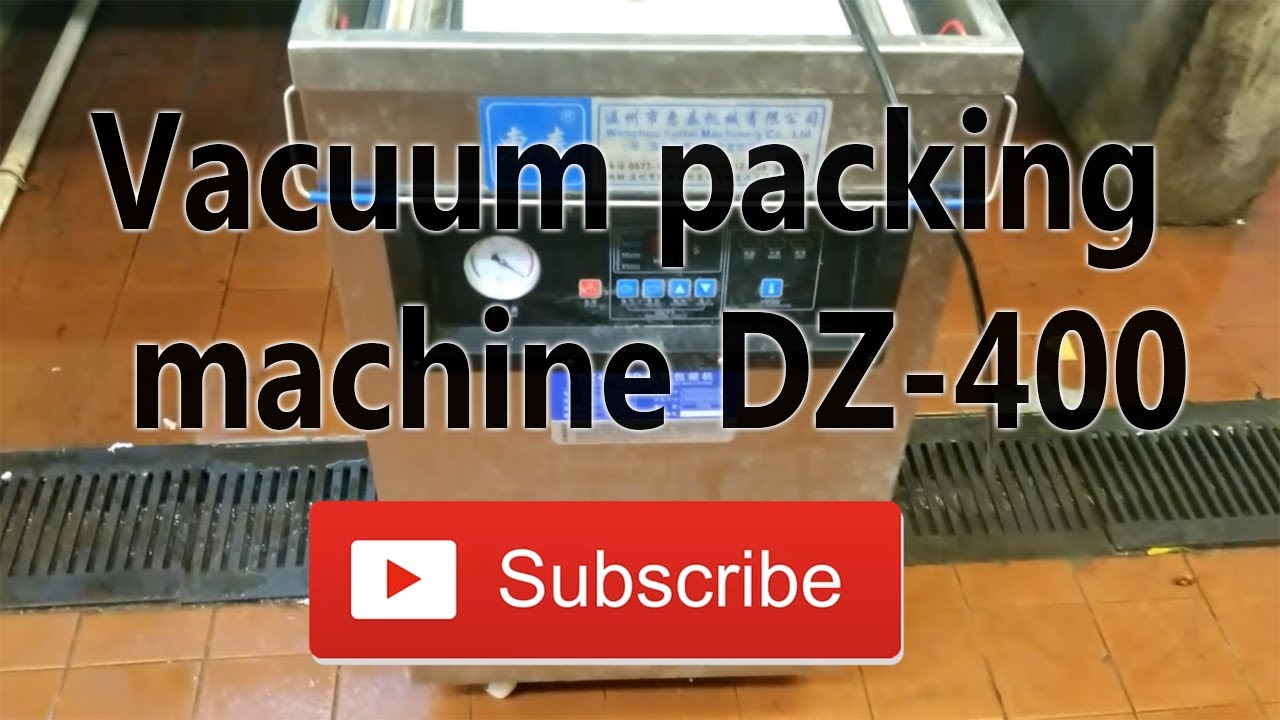